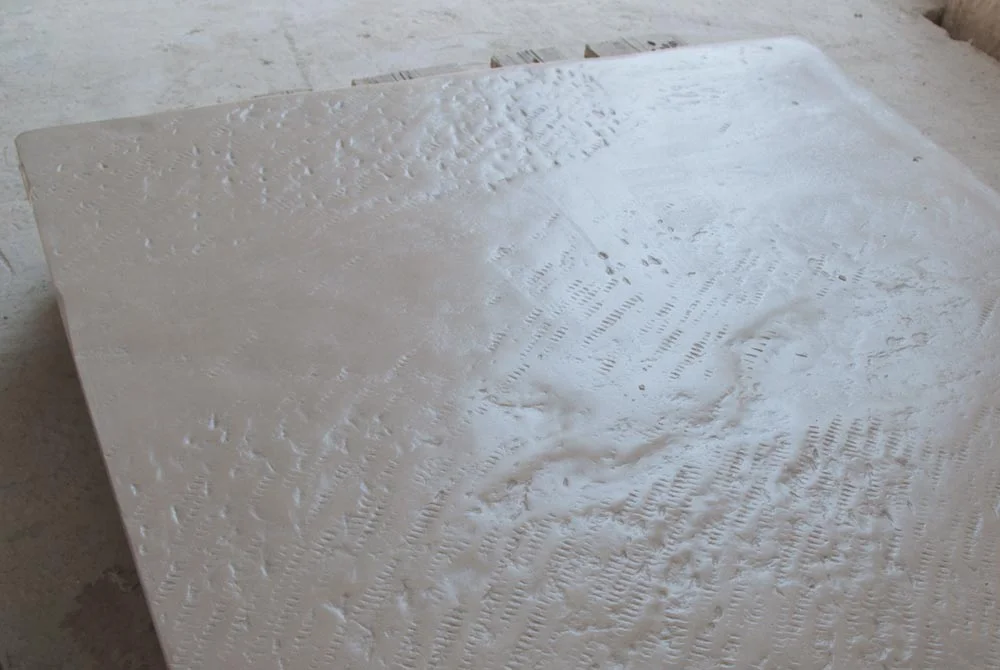
ΑΝΑΔΟΜΗΜΕΝΗ ΠΕΤΡΑ
Cast stone is a material made with natural aggregates and cementitious binder that is intended to resemble and be used in a similar way to natural stone.
What is cast stone?
Cast stone is created with the mixing and treatment of fine and coarse raw materials such as cement, sand, ground rock or grit. While maintaining the advantage of natural stone, cast stone enjoys many added advantages to those of natural stone.
It can be manufactured to imitate or recreate almost all natural stone.
It can be manufactured in any colour –bearing in mind that the material reacts just like natural stone and will portray faint differentiations.
It can be manufactured to have any surface texture – from smooth to rough.
It can imitate various level of corrosion, and is therefore suitable for renovations.
It is more resilient to cracking.
It can be more affordable that certain types of natural stone.
It can be moulded more easily to special constructions.
Cast stone is used worldwide as structural material for the creation of architectural details, facades, decorative products, floorings and for other applications in buildings and other structures.
Marathon Stone follows the Specifications for Cast Stone produced by the UK Cast Stone Association.
Read more about Marathon Stone specifications for the manufacturing of Cast Stone [PDF]
Production process
Marathon Stone uses two main methods of production depending on surface and structural requirements.
The semi-dry method
The semi-dry method, as the name implies, uses a low water content or ‘earth moist’ mix. The mix includes carefully selected aggregates, graded so that excellent compaction is obtained thus yielding very strong, dense products.
Compaction of the material is achieved using pneumatic hammers, ramming the material against stiff formers. After compaction the products are usually demoulded immediately. Depending on the difficulty and complexity of the shape it is possible to make considerable numbers of copies in an eight hour shift.
Dry cast stone units generally require very little surface finishing as the process itself produces a limestone like quality. However if necessary the surface can be tooled and sanded etc.
Curing is usually done in our direct fire steam curing chambers. This process produces very hard edges, greater impermeability, greater strength and tougher surfaces owing to carbonization.
The semi-dry method is most suitable for architectural items such as coping, cornices, balustrading, window and door surrounds etc. – also for garden ornaments such as, pots, urns, fountains, seating etc. Certain items wherever necessary can be reinforced.
Wet-cast method
This process uses a higher water content than semi-dry and results in a very dense product with a cube strength approaching 50Mpa or more.
Compaction is achieved using a combination of conventional methods – table vibration, poker or attached vibration or vacuum casting, the latter being used for relatively small items.
The wet cast method usually yields one piece per mould per day and this is always taken into account when calculating delivery deadlines.
Most products after demoulding are either tool finished, sanded, acid etched or otherwise treated to get the required stone texture.
Curing & Drying
Most of Marathon Stone products are cured in a special direct fire steam curing chamber built especially for us by Kraft Energy in Germany. Besides extremely effective curing, this process also hardens the surface of the products by carbonization.
If required we use gas fired drying chambers for preparation of products prior to sealing.